Rumored Buzz on Alcast Company
The 10-Second Trick For Alcast Company
Table of ContentsOur Alcast Company IdeasThe 30-Second Trick For Alcast CompanySome Known Questions About Alcast Company.Getting My Alcast Company To WorkGetting The Alcast Company To WorkAlcast Company - Questions
Chemical Comparison of Cast Aluminum Alloys Silicon promotes castability by reducing the alloy's melting temperature level and boosting fluidity during spreading. Additionally, silicon contributes to the alloy's strength and wear resistance, making it valuable in applications where resilience is essential, such as vehicle components and engine elements.It additionally boosts the machinability of the alloy, making it less complicated to refine right into completed products. By doing this, iron contributes to the total workability of aluminum alloys. Copper enhances electrical conductivity, making it useful in electric applications. It additionally boosts rust resistance and includes in the alloy's total strength.
Manganese adds to the stamina of light weight aluminum alloys and improves workability (Foundry). It is typically used in wrought aluminum items like sheets, extrusions, and accounts. The presence of manganese help in the alloy's formability and resistance to splitting throughout manufacture procedures. Magnesium is a lightweight component that offers strength and effect resistance to aluminum alloys.
The Ultimate Guide To Alcast Company
Zinc enhances the castability of aluminum alloys and aids regulate the solidification process throughout casting. It enhances the alloy's strength and hardness.

The main thermal conductivity, tensile strength, return stamina, and prolongation vary. Select suitable resources according to the efficiency of the target product created. Among the above alloys, A356 has the highest possible thermal conductivity, and A380 and ADC12 have the most affordable. The tensile restriction is the opposite. A360 has the very best return toughness and the highest elongation price.
The 5-Second Trick For Alcast Company
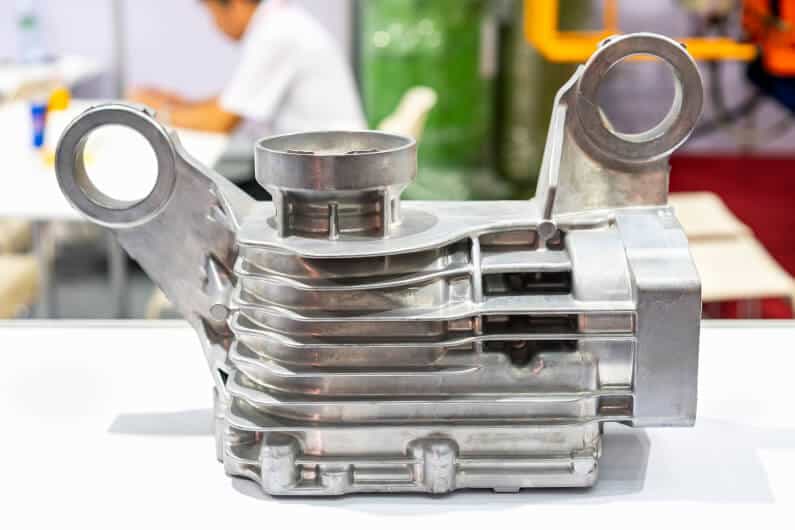
In accuracy spreading, 6063 is appropriate for applications where detailed geometries and premium surface area finishes are paramount. Instances consist of telecommunication enclosures, where the alloy's superior formability permits sleek and cosmetically pleasing styles while preserving architectural integrity. In the Illumination Solutions industry, precision-cast 6063 components produce sophisticated and reliable lights components that need complex shapes and great thermal efficiency.
The A360 exhibits premium prolongation, making it optimal for facility and thin-walled parts. In precision spreading applications, A360 is fit for industries such as Consumer Electronic Devices, Telecommunication, and Power Devices.
Indicators on Alcast Company You Should Know
Its distinct properties make A360 an important choice for accuracy spreading in these markets, improving product resilience and quality. aluminum metal casting. Light weight aluminum alloy 380, or A380, is a widely made use of spreading alloy with a number of distinctive qualities.
In precision casting, aluminum 413 beams in the Customer Electronic Devices and Power Devices markets. This alloy's remarkable deterioration resistance makes it an excellent selection for outside applications, guaranteeing long-lasting, durable items in the discussed industries.
Unknown Facts About Alcast Company
The light weight aluminum alloy you choose will substantially affect both the casting process and the buildings of the final product. Since of this, you need to make your decision carefully and take an informed strategy.
Figuring out the most suitable light weight aluminum alloy for your application will suggest weighing a wide selection of attributes. These comparative alloy features comply with the North American Pass Away Casting Association's standards, and we have actually divided them into two classifications. The first group addresses alloy characteristics that influence the manufacturing process. The 2nd covers qualities impacting the buildings of the last product.
The Ultimate Guide To Alcast Company
The alloy you find out here choose for die spreading straight impacts a number of elements of the casting procedure, like exactly how simple the alloy is to collaborate with and if it is prone to casting issues. Warm fracturing, also referred to as solidification breaking, is a typical die spreading flaw for light weight aluminum alloys that can result in inner or surface-level splits or fractures.
Specific aluminum alloys are much more at risk to warm cracking than others, and your choice should consider this. An additional typical issue found in the die casting of light weight aluminum is die soldering, which is when the cast stays with the die wall surfaces and makes ejection tough. It can damage both the cast and the die, so you must look for alloys with high anti-soldering buildings.
Corrosion resistance, which is already a notable feature of aluminum, can vary significantly from alloy to alloy and is an important particular to take into consideration depending upon the ecological conditions your product will be exposed to (aluminum metal casting). Put on resistance is another home frequently sought in light weight aluminum products and can distinguish some alloys